ECONOMICS OF A TRAGEDY: DID DUOPOLY BRING DOWN THE BOEING 737 MAX?
By Roger Morefield
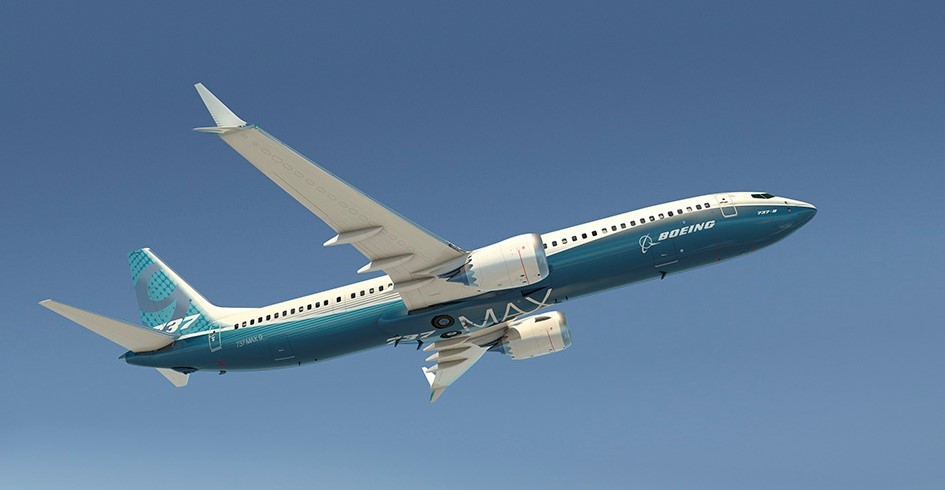
INTRODUCTION
This story begins in 1916, when businessman William Boeing wanted a plane to fly him from place to place among his business interests, but a satisfactory model was not available. So Boeing decided to produce his own. Over the next century, this effort evolved into the greatest airliner manufacturer of all time, the Boeing Company. Boeing’s products were so safe and well-engineered that many frequent fliers preferred to fly only on Boeing airliners, popularizing the saying “If it ain’t Boeing, I ain’t going.” Unfortunately, this era came to a tragic end in October, 2018.
Boeing’s venerable 737 model, the workhorse of today’s airliner fleet, made its first flight on April 9, 1967. In December 1967 Lufthansa and United Airlines added the first 737s to their fleet. Boeing has since upgraded the 737 numerous times with longer fuselages for more passenger capacity, improved aerodynamic wing designs, more advanced, powerful, quieter, fuel-efficient engines, improved airframe design, and upgraded avionics and flight-control systems. Airbus, then called Airbus Industrie, developed its A300 series airliners to compete with the Boeing 737. The first A300 entered commercial service in 1974, but originally didn’t sell well. However, by 2010 the re-engined Airbus A321, the A321neo [new engine option], had become a competitive threat to the Boeing 737. In 2006 Boeing was considering designing an entirely new plane to replace its flagship 737, but following the announcement of the A321neo, Boeing decided to re-engine its 737 as the 737-8 MAX, 737-9 MAX, and 737-10 MAX series. The MAX first flew in January, 2016 and entered commercial service in May, 2017. There were several incidents where on climb-out after takeoff the plane, without being prompted by the pilot, went into a shallow dive, but pilots were able to recover controllability by turning off trim control switches and in some instances turning the autopilot off and back on. Unfortunately, such incidents were not taken seriously enough, and pilots thought they were harmless incidences of an annoying but not deadly situation called “runaway trim.” On October 29, 2018, Indonesian airline Lion Air Flight 610 departed Jakarta and 12 minutes later plunged into the Java Sea at 450 miles per hour, with none of the 189 souls on board surviving. Back in the United States, Boeing and the FAA [Federal Aviation Administration] essentially blamed the flight crew and declared the plane was safe. No action was taken to ground the MAX at that time. Five months later, on March 10, 2019, Ethiopian Airlines Flight 302 departed Addis Ababa for Nairobi, Kenya. Six minutes later it crashed into a farm field 39 miles from the departure airport, killing all 157 people on board. The flight data that were immediately available showed an eerie similarity between the flight paths and maneuvers of both of the doomed aircraft. Again the FAA and the airlines defended the safety of the MAX. Three days later on March 13, after immense pressure from aviation safety officials all over the world, the FAA relented and grounded the MAX.
Large airliners are manufactured and sold by two firms, The Boeing Company and Airbus SE. These two firms have a combined 88% of the airliner market, making them a global duopoly. Duopolistic behavior is the extreme case of oligopolistic mutual interdependence, with both firms typically involved in intensive rivalry for market share.
These tragic events and the regulators’ and manufacturers’ responses to them raise a number of important questions. Did the duopolistic rivalry between Boeing and Airbus contribute in any way to this situation? Was the FAA’s reluctance to ground the MAX due to regulatory capture? How and why could not one, but two, of these crashes occur before this new version of an old design would be grounded to discover the cause? What impact would these events have on airline passenger perceptions of comfort and safety? Had the developing shortage of qualified airline pilots worldwide had an effect? Are 21st-century airliners too automated or not automated enough? What would be the eventual impact on Boeing as a company and on the airliner manufacturing industry as it strives to repair its damaged reputation? What is the potential impact on the FAA’s reputation as the global leader in airline safety regulation? And how can airlines across the world meet the challenges of an industry that was projected to grow at a compounded annual rate of 3.5% over the next two decades? This article addresses these questions as they relate to the duopolistic rivalry between Boeing and Airbus and assesses the extent to which this rivalry is implicated in the 737 MAX crashes and the irreparable losses sustained by the families of the 346 men, women, and children whose lives were untimely ended.
DUOPOLY
Duopoly is a special type of oligopoly market structure that is dominated by two sellers. Duopoly markets exist in the United States in carbonated soft drinks with Coca-Cola and Pepsi, free-standing retail pharmacies with CVS and Walgreens, home improvement stores with Home Depot and Lowes, common carriers with UPS and Fed Ex, credit card services with Visa and MasterCard, and wireless services with Verizon and AT&T. Given the 88% market share held by Boeing and Airbus, the global commercial airliner industry is a duopoly. Among several models that attempt to explain firm behavior under duopoly, the Cournot, Bertrand, and Stackelberg models stand out. Models of oligopoly are disappointing in that no single model best explains oligopoly behavior, and this is also true for duopoly. In the case of Boeing and Airbus, rivalry for market share seems to predominate. This rivalry is characterized by both firms’ efforts to have a product that fits the passenger capacity, fuel economy, range, reliability, ease of maintenance, and ease of pilot training needs of their airline customers just a little bit better than their rival’s product. Every year both companies aggressively vie for receiving the highest number of new airliner orders at the world’s largest air show, held in odd-numbered years at Paris’s Le Bourget Airport, and the world’s second-largest, held in even-numbered years at Farnsborough Airport in Hampshire, England. These air shows double as trade shows where aerospace/defense manufacturers display their wares in static displays and in flight as they attempt to book orders from likely buyers. Often the biggest news at the end of these shows is about the size of the orders each company got, either in number of planes sold or orders booked in billions of dollars or euros.
PRICING BEHAVIOR UNDER DUOPOLY
Boeing and Airbus engage in intense rivalry over price. Their pricing is complicated by the fact that new airliners are typically sold with a long lead time that can be five years or more. There is no such thing as buying a new commercial airliner “off the shelf.” That is, a plane ordered in 2019 might be delivered in 2024. Boeing and Airbus are known to steeply discount their planes off list price. For example, the Airbus A320neo and its direct competitor the Boeing 737 MAX 8 list for about US $110-120 Million, but may be sold for 45 to 55% less than that. This deep discounting allows the sellers some leeway to adjust the discounted price for inflation and currency fluctuations, if needed, during the long wait for delivery.
MEETING COMPETITION – REFRESHED OLD MODEL OR COMPLETELY NEW DESIGN?
A long-run strategic decision that may determine an airliner manufacturer’s survival is whether to freshen an existing model with new wings, avionics, engines, etc., or to design and develop an entirely new airplane. Designing a new airliner can cost more than $30 billion and take 10 years or more. An additional risk of designing a new plane “from scratch” is what may be thought of as the “Murphy’s Law” element – if anything can go wrong, it will. Boeing re-learned this lesson in designing the brand-new 787 Dreamliner to compete in the wide-body airliner market. “Wide-body” planes typically have two aisles in the passenger cabin with seating 3 abreast on the left, 3 or 4 abreast in the center, and 3 abreast on the right. The Dreamliner project began in 2003 and the plane first began commercial service in 2011, by which time Boeing had spent an estimated $32 billion on it. As of August 2019, Boeing had built 882 Dreamliners, still short of the 1,100 it needs to sell to turn a profit on the plane. And early on during commercial service the Dreamliner was plagued with fuel leaks, faulty wiring, and two cabin fires due to faulty lithium-ion batteries. The battery problem caused the Dreamliner to be grounded from January 2013 to April 2013. Given the risks of designing a new plane and the costs of doing so, refreshing an existing model to make it at least a bit better than its direct competitor appears to be a very attractive strategy.
THE BEGINNING OF THE END
Air disasters are usually the end result of an extended series of seemingly unrelated events that form a chain that eventually results in a crash. Factors that contribute to aviation accidents are equipment failure or malfunction, improper or inadequate maintenance, human error by air or ground crews, and unpredictable weather. Examples include improperly tightened screws on control surfaces, electrical wiring insulation that eventually wears thin and causes a short circuit, a faulty solder joint on a control board for a flight instrument, pilots missing an item on a pre-takeoff check list, mechanics rushing to get unsafe planes back in the air, pilots rushing to get the plane in the air to stay on or get back on schedule, and pilots flying into weather that is beyond the capability of the aircraft, the pilot, or both.
The MAX’s troubles are clearly rooted in the interdependence between Boeing and Airbus. Undoubtedly Boeing felt the necessity to abandon plans to design a brand-new replacement for its classic 737 as Airbus had turned on the competitive “heat” by re-engining its A320 models to strengthen its position against BoeingThe “bypass ratio” of a jet engine is the amount of air passing around the center of the engine as a multiple of the amount going directly through the engine’s center. With higher and higher bypass ratios, the newer engines are larger in diameter and require more space to fit under the wing of the airplane. One of Boeing’s objectives for the re-engined 737 MAX was that it would handle so much like the 737s already in service that the FAA would not require additional pilot training. Airlines have an incentive to have a fleet of planes whose flight handling characteristics are so similar that any of their pilots could fly any of their fleet without additional specialized training. This was a strong selling point for getting orders for the new MAX. Pilot training is expensive and consumes pilot time that could otherwise be used to produce revenue. So Boeing’s airline customers were happy to get a larger-capacity, longer-range, more fuel-efficient airplane for their fleets that didn’t require additional pilot training.
But the newer engines on the MAX are so large in diameter that they had to be moved forward under the wing to maintain the necessary ground clearance. With higher thrust coming from further forward under the wing, the re-engined MAX had a tendency to assume a “nose-high” attitude under certain conditions, such as on takeoff, when maximum power is applied. At this point, Boeing made a strategic decision that marks the beginning of the series of events that brought down Lion Air 610 and Ethiopia Air 302. Rather than do some major redesign to make a more stable plane, Boeing decided on a software “fix.” A software fix was attractive because it didn’t require any airframe redesign and the billions of dollars and years of delay that could result. In addition, software is cheap and doesn’t weigh anything, so additional software doesn’t raise production costs or reduce the plane’s payload.
The software fix for the MAX’s “pitch-up” tendency is called the Maneuvering Characteristics Augmentation System (MCAS). The MCAS was designed to run in the background without the need for activation by the flight crew. It was only active when the plane’s autopilot was off, that is, when it was being flown manually. MCAS took its input from a small vane on the outside of the fuselage called an Angle-of-Attack (AOA) sensor. The angle of attack is the angle between the chord of the wing and the relative wind. When the angle of attack gets too high, the air passing over the wing becomes turbulent and ceases to develop enough lift to keep the plane in the air. This is known as a stall. With proper and prompt pilot response and sufficient altitude, it is possible for an 88-ton airliner to recover from a stall, but a stall is extremely dangerous and should be avoided at all costs. The MCAS was programmed such that, on sensing a dangerously high angle of attack, it would move the controls to push the nose down without any pilot input. And the designers of the system assumed, apparently incorrectly, that if the MCAS malfunctioned the pilots would react as they had been trained to react in a so-called “runaway trim” situation. Therefore, incorrect assumptions by the designers about typical pilot response to an MCAS malfunction were another link in the chain of events leading to disaster.
Another incorrect assumption made by the designers of the MAX, and perhaps due to pressure from company management, was that an MCAS malfunction or failure was so remotely improbable that they saw no need to mention it in the original operations manuals. It was feared that information about the MCAS in the operations manuals would attract unwanted attention from the FAA, thus slowing the certification process and perhaps giving the FAA reason to require additional pilot training for the MAX. This would have defeated Boeing’s desire to promote the MAX as needing no additional pilot training, which was a very important selling point.
THE VERY COSTLY RESULTS
The story of Boeing’s role in the tragedies of Lion Air 610 and Ethiopia Air 302 is still being written but many lessons can be learned from it now. It is thought by some industry observers that Boeing began to lower its standards when it merged with McDonnell-Douglas in August of 1997. The share price of Boeing stock [NYSE: BA] just prior to the merger was $35. It was at an all-time high of $401 in February 2019, just days before the Lion Air crash. As of early March 2021, it was at $224. Boeing’s market capitalization fell from $184 billion to $124 billion during this period.
A lesson that companies need to re-learn again and again is “stick to your knitting.” That is, stay with those things that made your company great. Beginning with the August 1997 merger with McDonnell-Douglas, Boeing began to focus more on enhancing its bottom line than on designing and manufacturing the world’s best airliners. History is replete with stories of companies that didn’t stay with what made them great and now either no longer exist or are a shell of their former selves. General Motors’ share of the US auto market has fallen from about 50% in the 1950s to the 17% that it is now. Long ago, GM strayed from its emphasis on quality and innovation, and is now struggling to compete effectively in burgeoning markets for autonomous and electric vehicles. Has the tragedy of the Boeing 737 MAX brought Boeing to repentance on this? For the sake of the flying public, and indeed for all of Boeing’s stakeholders, one can only hope so.
Another important lesson for management is to avoid what Columbia University sociologist Diane Vaughan called “normalization of deviance” in her study of the events leading up to the catastrophic failure of the O-rings on the solid rocket boosters of space shuttle Challenger. Challenger exploded 73 seconds into its launch on January 28, 1986. Morton Thiokol, the NASA contractor on the O-rings, initially refused to certify them to perform properly at temperatures below 53° Fahrenheit. The ambient air temperature at launch was 36°F and had been as low as 26°F the night before. In The Challenger Launch Decision, Professor Vaughan described the process by which Morton Thiokol was pressured by NASA, in its desire to stay on schedule with the mission, to sign off on the launch in spite of the low temperatures. In addition, there had been several previous troubling incidents with the O-rings which, in hindsight, clearly indicated their need to be re-designed for greater safety at lower temperatures.
The tragedy of the Boeing 737 MAX speaks volumes about public policy-making. “Regulatory capture” can be defined as a situation that occurs when a government regulatory agency ends up being controlled by the industry it is supposed to be regulating. There was certainly a need for close collaboration between Boeing and the Federal Aviation Administration (FAA) concerning the airworthiness of the MAX, but that relationship appears to have been much too close. This may be the reason why, inexplicably, the FAA didn’t ground the MAX in October 2018 after the Lion Air 610 crash. Other examples of regulatory capture include the relationship between the pharmaceutical industry [“Big Pharma”] and the U.S. Food and Drug Administration. And in Texas, a faulty relationship between the state’s Electric Reliability Council of Texas (ERCOT) and electric generating companies in the state was a key factor in the deadly and embarrassing failure of Texas’ power grid during the winter storm of February 2021.
Another question raised in the Introduction is about airliner automation. This is an ongoing controversy that isn’t going to end soon. There is a rumor circulating that Airbus CEO Guillame Faury said he wanted Airbus products to be so easy to fly they could be flown by his concierge! Whether the quote is true or not, the idea has annoyed a great many people. Would you rather fly in an airliner where the control surfaces are actuated manually from the cockpit by cables and levers, or by electronic signals to servomotors to move the controls? There are strong arguments on both sides. Advocates of manual controls assert that pilots need to manually “hand-fly” the plane in order to maintain their flying skills and just to have a feel for how the airplane is responding. Advocates of “fly-by-wire” contend that it provides an extra layer of safety that can’t be incorporated into manual systems of control. In fact, this is a major difference between Boeing and Airbus products. Boeing airliners still have the traditional control yoke, while the Airbus has a “sidestick,” a device resembling the “joystick” controller found on video games. Boeing airliners do have wires and cables that move the control surfaces, but these are augmented by electric servomotors and hydraulics. The relationship of this controversy to the 737 MAX tragedies is illustrated by the MCAS malfunctions that brought down Lion Air 610 and Ethiopia Air 302. This may signal that too much automation can be as bad as not enough. The automation discussion continues.
CONCLUSION
Nearly two years after it was grounded, the MAX re-entered regularly scheduled service again with an American Airlines flight on December 29, 2020. American and the other U.S. legacy carriers are being very mindful of passenger sentiment about the MAX as they slowly re-introduce it into their regular schedules. Due to the changes that were made to get it re-certified by the FAA, the MAX is very safe, no doubt safer than it was before 2019. But many questions remain. Will Boeing, its airline customers, and the U.S. FAA learn the lessons that need to be learned from the twin tragedies of Lion Air 610 and Ethiopia Air 302? It is then, and only then, that something good can be said to have resulted from this tragic chapter in the history of global commercial aviation.
Roger Morefield
Associate Professor of Economics